Gavin Hartley from Blackhead Quarries presented his Quarrying Way Down South paper to the Institute of Quarrying Otago/Southland Branch mini conference held in Gore 23-24 July 2020. His paper was a favourite with the delegates and the IoQ nominated Gavin for the 2021 Caernarfon Award, which he won. This is a precis of his entry.
Quarrying in an isolated place and in adverse weather conditions is very challenging and this paper provides a snapshot of a small team of quarrying professionals producing aggregate for new building foundations in one of the world’s harshest environments – way down south at McMurdo Station in Antarctica.
My story started with a phone call in September 2019; “We’re looking at a job in Antarctica, do you want to go?”
Well, I don’t have a bucket list, but if I did, it would be one place in the world I would have on it. And I continue to be amazed while talking with fellow quarrymen to learn of all the weird and wonderful places we get to crush rock, and the innovative methods we come up with to crush all the different types of rock around the world.
The background
Fulton Hogan had been asked by the United States Antarctic Program (USAP) to provide expertise in quarrying and crushing rocks. The Americans have their Antarctic Program base in Christchurch and, like many projects, it’s not a case of what you know – it’s a case of who you know and a conversation in a pub one night.
I assume that my name come up in that conversation because I studied as a geologist many moons ago and have been involved in quarrying for 30 years on various projects in New Zealand and the Pacific Islands. At the time, I managed Blackhead Quarry in Dunedin, a basalt quarry, similar (but not quite the same as it pans out) to the rock around McMurdo Station in Antarctica.
I was part of a two-person team sent to evaluate potential quarry locations and review any risks sending staff to McMurdo Station. Michael Earnshaw was the other member, who was the quarry manager at the Miners Road Quarry in Christchurch. Tim McMorran from consulting environmental engineers, Golders, also accompanied us as he had experience on the ice and had previously worked with the team at McMurdo.
McMurdo Station is the main US station in Antarctica, at the southern tip of Ross Island, about 3800 kilometres south of Christchurch and 1360 kilometres north of the South Pole.
The area on which the station is built is on a gentle slope, facing the Ross Sea. It was first established in 1955 and since has had buildings added, but with no real town planning taken into consideration. Currently there are approximately 100 buildings scattered around the station in various states of repair and with some not used for their original purpose.
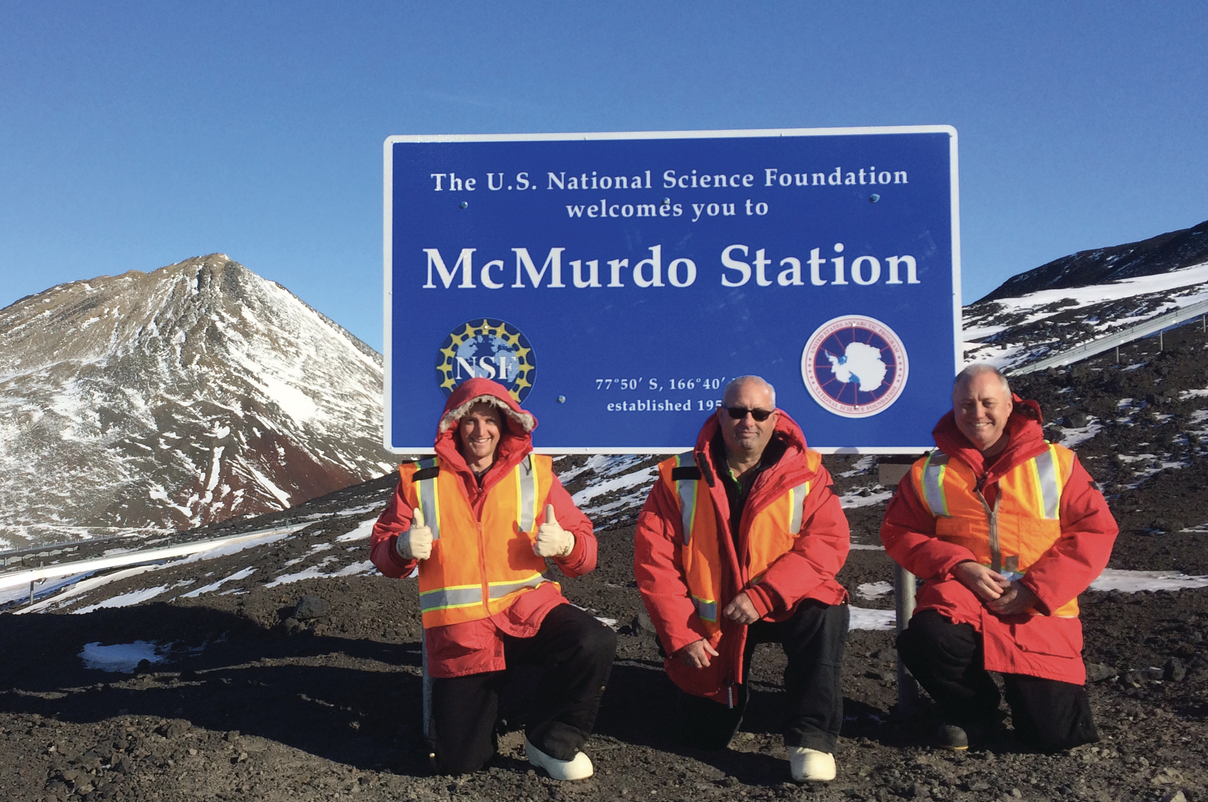
The project
The USAP required aggregate for the Antarctic Infrastructure Modernisation for Science Project (AIMS). This project aims to construct a number of modern, multi-storey, energy-efficient buildings, to replace the majority of the existing buildings on the station.
The aggregate, of course, is required to construct building platforms for six main blocks of buildings with associated utilities and project works such as site drainage.
The journey
Before you even step on the ice there is a rigorous Personal Qualification (PQ) pre-deployment process. This includes doctor and dental consultations with blood tests, along with a flu injection. The PQ needs to be carried out well in advance of deployment, prior to booked flights and accommodation in Christchurch.
Our flight departed Christchurch 20 October 2019 after a number of weather and technical delays, including a cracked windscreen on the C17 military jet plane that was to take us to the frozen continent. The flight took 4.5 hours and was the fourth of that summer season, so every available space was taken – 120 passengers and freight.
On arrival, the cold takes your breath away; there’s the crunch of ice underfoot; and the immense white snow and ice panorama as far as the eye can see. The runway is built on continental sea ice. Due to their weight the C17s can only land on the ice for a few months of the year. For the remaining daylight months of the year a C130 Hercules takes over with a bone shaking 8.5-hour flight.
Life on base was very regimented and begun with the first of many health and safety inductions. A permit system was used to carry out almost all activities while on the ice. Permits were required to drive specific vehicles, for Outdoor Survival Safety to walk outside of the station limits, and additional permits to walk beyond to the sea ice. Emergency preparedness was also extremely important in one of the world’s harshest environments.
Once inductions were completed it was time to get to work in an action packed five days on the ice.
Aggregate production and equipment
Prior to this project, aggregate production at McMurdo was ‘third world’, although with the luxury of earth moving machines.
A number of static grizzly screens had been used to produce three different sized aggregate. The rock to be screened was produced during the summer season where a Cat D9 bulldozer would push the top 200mm layer down to the screen where a wheeled loader would run the material over the grizzly screens.
The reason for only 200mm in depth being processed was everything below that level was frozen and too hard, even during the summer months.
The AIMS project required 66,000 cubic yards of 2.5-inch aggregate. Now, if you are anything like me brought up in a metric world these imperial measurements took some figuring out. I remember sitting in meetings with the client, building contractor and engineer trying to convert these old measurements back to more familiar metric numbers. Whether imperial or metric, it was clear that this volume (55,500 cubic metres) was not going to be produced by a static grizzly.
Leidos was the main contractor to the National Science Foundation (NSF) which runs the USAP. It had purchased some state-of-the-art Metso equipment from Wagner Equipment back in the US.
Leidos purchased a Lokotrack LT106 jaw crusher, LT200HP cone crusher, and a ST3.8 mobile screen for the AIMS project to be shipped to Antarctica. The plant had been fitted for extreme cold conditions (minus 40C), fitted with extra insulation and immersion heaters, and low temp oils and to run on a diesel/kerosene blend. The production target for the plant was 250 tonnes per hour of 63mm crushed stone.
I had actually be on a Mimico/Metso customers’ tour and met the team from Leidos and had seen the jaw and cone crushers in the factory in Tampere, Finland, only days before they started their journey to the ice.
The quarry site
Our initial investigation started with selection of a site to open a quarry and Leidos staff on site had short listed three potential locations.
Snow and ice covered all the sites with only minimal exposure of rock, although it soon become apparent all the rock was volcanic with a loose description being basaltic in nature. Unlike most locations around the world, there was no weathering profile; the only alteration was due to freeze thaw cycles although this only affected the top 200 – 300 mm. The rock below this level remained frozen.
A major consideration for opening a quarry was given the pristine environment and the USAP wanted to minimise the foot print around the base. Grey’s Chute was chosen as the preferred site due to its close proximity to where the aggregate was required, and the chute had traditionally been used to provide material to run over the static grizzly screens.
Once the quarry was sorted, we met the National Science Foundation (NSF) Station manager who was a US marshal who had been the station manager for a number of years. We visited the team leaders from the hospital, fire house, health and safety, environmental, communications, workshop and most importantly – fleet operations. And all were more than welcoming. Everybody was aware of the AIMS project and their attitude was that the upgrade was required and if a jaw crusher had to come in and crush rock in the middle of the station then it would happen.
The hospital had a four-bed ward and two-bed emergency room, x ray, bloods lab, physio-therapist and, in the peak of the season, there were five medical staff at the hospital. Slips, trips and falls were the main injuries presented at the hospital. Interestingly, the most qualified medical person on base was washing dishes in the cafe. Like many people on base, they simply wanted the experience of working in Antarctica.
And you met people from all walks of life not doing what they trained to do in mainland USA. The fire department was well-equipped like any you would find in a medium sized town in New Zealand. The majority of their call outs were for spills and a spill of a cup or more initiated an emergency response, and with a thorough investigation and associated reports. Their major issue was the lack of water for firefighting, so response time was extremely important. The Fire House workshop was like any you would see here, fully equipped with spares, tool store and hydraulic shop.
Fulton Hogan staff would be working very closely with the Fleet Operations department. As the name suggests they managed and operated the heavy equipment – the excavators, bulldozers, trucks, graders and drill that would work in the quarry.
The weather
Weather impacts nearly everything at McMurdo Station, especially with respect to safety and logistics.
Weather is classified into three conditions. Condition three is normal weather; in Condition two you must check out with the firehouse by radio prior to leaving McMurdo and check in upon return; and with Condition one only mission-critical travel is permitted, which requires approval from the NSF station manager.
We only experienced Condition three weather, although even with the sun out, if it got windy the wind chill could make a pleasant day very uncomfortable. Typical day time temperatures were minus 18 degrees Celsius with a wind chill of minus 28 degrees Celsius. Any exposed skin needed to be covered. As an example of how bad the weather can get, there were ropes strung between buildings at each external door when it turned Condition 1, as wind and white-out conditions made it extremely difficult moving between buildings.
Becoming tourists
Once our work was completed, we were treated to some of the highlights of the area. Our hosts took us around the Crary Science and Engineering Centre and we saw a number of experiments that were taking place.
Most of the sea creatures can be found in other parts of the world although in Antarctica they are in miniature form. We visited inside Robert Falcon Scott’s hut that has been preserved as if he had just walked out yesterday.
There’s a limited entry of 1500 people per year allowed into the hut but even rich tourists can pay thousands of dollars to go to Antarctica and not set foot on land due to the weather. Being a Kiwi the highlight for me was visiting Hilary’s Hut at Scott Base (The only New Zealand base in Antarctica) and sitting in Edmund Hilary’s favourite chair where he planned his expedition in tractors to the South Pole.
The crushing team
The Metso Mobile Crushing equipment arrived by sea in January 2020; the crushing team arrived shortly after we had settled in.
Craig Upston was an important member of the team. He is the quarry manager at Blackhead Quarries, a hard rock quarry in Balclutha located about 80 kilometres south of Dunedin. Craig had recently taken delivery of the same model jaw and cone crushers that were to be used on the ice.
Prior to departing New Zealand, the crushing team spent time crushing at the Balclutha Quarry to familiarise themselves with the equipment and, more importantly, to get to know each other so they knew they could work with each other. Positive personal relationships are critical when working, eating, and living together in such a remote location. There was no opportunity to hop on a bus and go home!
The Fleet operation team (at McMurdo Station) had started developing the quarry before the Fulton Hogan Crushing team arrived.
Most of the rock had been blasted. An Atlas Copco T45 top hammer rig had drilled the holes, and packaged explosives were initiated with Nonel detonators supplied from New Zealand. Normally the drill rig and explosives were used for blasting ice that had formed pressure ridges in the sea ice across the many ice roads out from the base.
The Americans love their bulldozers and by the time we got to crush the rock it had already been moved some distance with dozers which is not the best scenario for crushing. It took some time to convince them not to stockpile great quantities of crusher feed.
Like all new quarries it took time to work out the best way to produce the AP65 (2.5-inch). The team found that the most efficient way was using a Cat 323 excavator to feed the LT106 jaw linked with the LT200HP cone and loading out with a Cat 972 wheeled loader. This meant the ST3.8 screen was not used all the time. In some ways this was good, as it was one less piece of equipment to keep an eye on.
There was a specification for the AP65 and testing was carried out, although producing enough fines through the cone wasn’t always easy and you can only do so much with the feed rock you are provided. The aggregate was fit for purpose to construct the building pads. Some of the blasts contained boulders too large to be put in the jaw but these were frozen lumps of basaltic rock and not your typical oversize.
Other than the extreme cold weather, it was just like crushing anywhere else in the world. If all was going well, you could sit in your heated cab and watch the plant run. Like we all know if crushing was easy everybody would be doing it. It is when things go wrong and you must get out of your heated cab that things become difficult. First, you need to get heavy coats, gloves, face protection on before leaving the cab, then negotiate icy rock to fix the problem. And some problems just had to wait until the wind died away.
All equipment required a long pre-start warm up before they got to operating temperature. The cone crusher was the most susceptible to cold weather and its warmup could take up to 90 minutes to heat the oil in the tank. Warming up the machinery was done with warm air blowers, along with turning the oil pumps on to circulate the oil in tank.
Some problems that were expected never eventuated. For instance, back home drive belts slip and conveyor belts ice up and slip. Since there is no moisture in the air in Antarctica, we didn’t experience belt slip.
Although, the lack of water made life difficult for constructing the building pads as there was no water to aid in compaction.
A typical day started at 6am and finished at 4pm with production very dependent on the weather. The crushing team worked closely with the fleet operations team but, due to its efficiency, the crushing plant was only operated on day shift, whereas the Fleet operations team worked 24/7. I should add that ‘day shift’ is only a relative concept as during summer the sun never goes down and in winter the sun never comes up.
While on the first deployment the team crushed AP20 using the ST3.8. This was mainly used for roading and stemming blast holes.
Aggregate had never been stockpiled in Antarctica due to production capacity. The thought was the stockpile would turn into one big lump of frozen aggregate and this did occur with the AP20.
A unique experience
The summer season at McMurdo Station is from October to April and during this time 1200 people can stay or pass through the station with only around 80 people wintering over. For every scientist the station has one support person providing logistical support.
As expected, the great leveller was the weather, or more precisely the wind. The sun could be out and if the wind was blowing it made life very uncomfortable.
The isolation and being away from family were also a major consideration. Typically, on project work you could be away for a few weeks whereas a season on the ice could be a few months with very limited flights back to New Zealand and, if the weather was rough, flights could get delayed.
Covid has meant the AIMS project has been put on hold and the second deployment to Antarctica will start once travel frees up.
Like all projects we have learnt a lot in a short period; not only on how to best operate the crushing equipment and produce aggregate, but that selection of staff is key to a successful deployment.
It is all very well wanting to go and experience Antarctica, although you cannot underestimate that life on the frozen continent is demanding both physically and mentally.
You can purchase the most expensive and best equipment in the world but having great people to operate that equipment is the key.
Acknowledgments
I acknowledge Craig Upston, Blair Ferguson, Quinn McNab and Murray Discombe in helping me write this report and supplying some brilliant photos. Without their help this report would not have been possible.
A winning entry
Since 1989 the Caernarfon Award has been presented annually for the best paper given at an Institute of Quarrying conference, seminar, or meeting anywhere in the world which is adjudged to have contributed the most to the advancement of some aspect (technical, environmental, strategic) of the quarrying sector.
The winner and runners up of the 2021 Caernarfon Award are judged by the presidents of the international Institute of Quarrying (IQ) branches (United Kingdom, Southern Africa, Hong Kong, Malaysia, Australia and New Zealand).
Gavin Hartley MIQ, Quarry Manager Blackhead Quarry, Dunedin, was the 2021 winner, and the award was presented at QuarryNZ Conference Awards Dinner held in Wellington on 16 July 2021. His presentation ‘Quarrying Way down South’ highlighted the challenges of quarrying in one of the world’s harshest environments, and the international IoQ presidents recognised that Gavin also demonstrated how IoQ members share their skills and expertise with colleagues and other professionals around the world, while at the same time expanding their own.